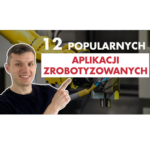
Najpopularniejsze aplikacje zrobotyzowane w obszarze automotive – to temat dzisiejszego odcinka.
Ostatnio mówiłem o najważniejszych przesłankach do robotyzacji i automatyzacji. Pewnie można znaleźć ich więcej, ale wymieniłem ostatnio osiem najbardziej istotnych według mnie.
Dziś będziemy mówić z kolei o tym, jak to wygląda w praktyce, czyli omówimy przykłady najpopularniejszych aplikacji zrobotyzowanych.
Nie będzie tu podziału na Polskę, Europę, świat – robotyka jest wszędzie taka sama. Ogólny udział w rynku poszczególnych aplikacji może się trochę różnić w poszczególnych krajach.
Podstawowym czynnikiem jest najczęściej struktura produkcji i przemysłu jako ogółu. Kraje, w których PKB najmocniej zależy od automotive, siłą rzeczy będą miały największy odsetek aplikacji zrobotyzowanych właśnie w tym obszarze.
W Polsce automotive generuje około 8 proc. PKB – to mniej więcej tyle, co w Niemczech, ale istotnie mniej niż np. w Słowacji, gdzie jest to około 13%. I tam robotyzacja faktycznie ma głównie twarz przemysłu samochodowego.
Jednak nawet w obszarze automotive możemy mieć do czynienia z bardzo zróżnicowanymi typami aplikacji. Dziś postaram się krótko omówić 12, subiektywnie, najpopularniejszych i jednocześnie definiując te aplikacje w oparciu o te same kryteria.
Aby nie przeciągać – zaczynajmy.
Nie spotkałem w polskim internecie podziału typów aplikacji zrobotyzowanych, który uznałbym za jednoznacznie merytorycznie właściwy. Dlatego właśnie, w oparciu o własną wiedzę i doświadczenie stworzyłem swój własny podział, który jest, wg. Mnie, najwłaściwszy pod kątem znanej mi teorii inżynierii. Tym samym wyróżniamy 4 podstawowe typu aplikacji zrobotyzowanych. Są to aplikacje:
- Handlingowe
- Montażowe
- Technologiczne
- Inspekcyjno-kontrolne
Zacznijmy więc po kolei – od aplikacji handlingowych.
Najpopularniejszy przykład handlingowej aplikacji zrobotyzowanej to… Pick&Place
Określany również, właśnie wymienionym wcześniej staropolskim słowem – handling.
Mowa jest tu o wszystkich typach aplikacji w których głównym zadaniem robota jest pobrać produkt, przenieść go w inne miejsce i tam odłożyć. Całość odbywa się ze zmianą lub bez zmiany orientacji produkcji. Na przenoszonym produkcie najczęściej nie są wykonywane żadne dodatkowe operacje. Jest to najprostszy typ aplikacji zrobotyzowanej.
Narzędziem jest tu najczęściej chwytak – siłowy lub kształtowy. I tu wymagane jest trochę teorii więc pozwolę sobie na te merytoryczną chwilę dygresji.
W robotyce są to bowiem jedyne dwa sposoby chwytu.
Chwyt siłowy tzn. taki, który utrzymuje przenoszony przedmiot poprzez działanie na niego siłami adekwatnymi do przeciwstawnych sił próbujących wyrwać przedmiot z obecnego położenia. Przykładami takich chwytaków są na przykład (w aplikacjach typu pick&place):
- Chwytaki magnetyczne do łapania elementów ferromagnetycznych
- Wszelkiego typu pneumatyczne chwytaki typu smart o kontrolowanej sile chwytu,
- Chwytaki podciśnieniowe w postaci przyssawek lub całych ich zespołów – np. Do przenoszenia tafli szkła lub kartonów.
Chwyt kształtowy to taki w którym sam kształt chwytaka uniemożliwia przemieszczenia się obiektu chwytanego w wybranych lub wszystkich osiach. Przykładem takiego chwytu jest np. Chwyt pryzmatyczny do elementów osiowo symetrycznych (tzn. np. Wałków)
Bardzo często, budując chwytaki, łączy się oba te sposoby chwytu w budowie chwytaków aby zapewnić maksymalną pewność orientacji przedmiotu przenoszonego.
Wracając do samej aplikacji typu pick&place.
Pod kątem sterowanie totalnie najprostsze aplikacji ograniczają się co najwyżej do wymiany pojedynczych sygnałów z otoczeniem. Mowa jest tu o sygnałach z czujników informujących o obecności produktu w miejscu pobrania oraz odłożenia. Tego typu proste aplikacje nie wymagają rozbudowanych systemów sterowania i nierzadko wystarczającym może się okazać sterowanie i dostępne wyspy I/O robota.
Taką aplikację można jednak we względnie dowolny sposób „komplikować”.
Dobrym przykładem dość wymagającej aplikacji typu pick&place są maszyny i stanowiska kompletacyjne.
Wyobraźmy sobie bowiem kompletacje bombonierki o różnych smakach. Wszystkie smaki czekoladek jadą zmieszane na jednym przenośniku. Na drugim przenośniku leży foremka bombonierki. Oba przenośniki dzieli tylko stado robotów.
System wizyjny rozpoznaje czekoladki. Z kolei zewnętrzny lub zintegrowany system nadążny aktualizuje pozycje rozpoznanej czekoladki w funkcji prędkości taśmy – to właśnie dzięki takim rozwiązaniom robot trafia bezbłędnie w czekoladkę, która jeszcze przed chwilą była kilka cm wcześniej. Już na etapie rozpoznania pojedynczej czekoladki system wie w której formie i jakim miejscu ma się ona znaleźć – to zapewnia koordynaty końcowe robota niosącego wspomnianą czekoladkę, która bezbłędnie ląduje w formie. Dodatkowo całość spina nadrzędny system sterowania posiadający informacje np. O planie produkcyjnych i charakterystykę każdej możliwej konfiguracji bombonierki.
To już bardzo rozbudowany, skomplikowany i drogi system. Ale to dalej pick&place.
W takim przypadku jak opisałem przed chwilą, najlepiej sprawdzają się roboty zdolne do bardzo dynamicznych przemieszczeń czyli przede wszystkim kinematyki typu scara lub delta. Nowe roboty tego typu mogą osiągać do ponad 60 cykli na minutę. W tego typu robotach praktycznie nie da się wykonać wieloosiowej reorientacji przedmiotu. Można dokonać obrotu jedynie w osi poziomej.
Gdy więc mówimy o aplikacjach, które wymagają reorientowania przenoszonego przedmiotu w wielu kierunkach zastosowanie znajdują tu roboty o kinematyce przegubowej – najcześciej 6-osiowej, które dysponują jednak znacznie mniejszą dynamiką ruchu.
I tu znowu mała dygresja definicyjna. Gdy mówię o dynamice ruchu mam na myśli zdolności szybkiej zmiany kierunku, startu i przyspieszeń. Do takich manewrów stworzone zostały roboty o kinematyce typu Delta i Scara. I choć prędkości liniowe robotów przegubowych, 6-osiowych, nie odbiegają, a czasem nawet przewyższają te małe, szybkie roboty typu Scara i Delta to jednak nie ma tu mowy o tak dynamicznych zwrotach akcji. Kinematyka przegubowa to większy udźwig, masa i więcej mechaniki – nie tak łatwo tym sprawnie wystartować.
Wracając jednak, ponownie, do pick&place. W nieco mniej skomplikowanym przenoszeniu. Szczególnie takim gdy liczy się duża elastyczność, pojawiają się częste zmiany, robot musi pracować blisko ludzi a wydajność nie jest najwyższym priorytetem bardzo dobrze sprawdzają się roboty kolaboracyjne. I to właśnie tego typu aplikacje i ich odmiany zapewniły cobotom miejsce w dzisiejszej robotyce.
Pewną odmianą procesu typu „pick&place” jest też oczywiście paletyzacja ale i o niej za chwilę słów kilka.
Skoro już wspomniałem o systemach wizyjnych to nie mógłbym nie wspomnieć o aplikacjach kompletacyjnych.
Kolejną, specyficzną odmianą aplikacji typu handling jest bowiem binpicking.
Jest to aplikacja zyskująca ostatnimi laty na tyle duża popularność, że uznałem iż nie można jej pominąć i należy poświęcić jej kilka słów.
Chcąc wytłumaczyć czym jest binpicking trafiłem na definicje jednego producentów systemów wizyjnych używanych w tego typu rozwiązaniach, której prostota szczególnie przypadła mi do gustu.
BIN PICKING to technologia, w której robot wyposażony w kamerę 3D, wyjmuje detale z pojemnika wypełnionego w nieuporządkowany i często nieregularnie ukształtowany sposób, a następnie podaje je w odpowiedniej orientacji do dalszej obróbki. Wyzwaniem jest szczególnie wyjmowanie z kontenerów obiektów o różnych kształtach, które umieszczone są w pojemnikach całkowicie chaotycznie.
Definicje przytoczyłem w całości ale warto zaznaczyć, że nie zawsze musi to być obróbka. Celem rozpoznawania i kompletacji elementów może być dowolny proces następujący za stanowiskiem binpickingowym. Może to być proces zarówno mantażowy jak i kontrolny a nawet transport.
Aplikacja ta jest szczególnie popularna w automotive i wszędzie tam gdzie mamy do czynienia z produkcją gniazdową a części są buforowane w zapasach międzyoperacyjnych. Dzięki zastosowaniu stanowisk binpickingowym człowiek eliminowany jest z elementu procesu nie przynoszącego wartości dodanej produktowi.
W tego typu aplikacjach rodzaj i sposób działania chwytaka jest bardzo silnie uzależniony od kształtu przedmiotu i poziomu jego nieuporządkowania w skrzyni lub opakowaniu. Przy większym poziomie uporządkowania stosuje się chwytaki kształtowe i kształtówo-siłowe. Dla totalnego chaosu chwytaki typowo siłowe – np. Magnetyczne i podciśnieniowe.
Integralną częścią systemu binpickingowego jest system wizyjny 3D pozwalający na rozpoznawanie elementów pobieranych z jednoczesnym, jednoznacznym określaniem ich położenia i orientacji w przestrzeni. Tego typu system 3D jest najczęściej gotowym rozwiązaniem z własną jednostką centralną dzięki czemu nie ma potrzeby integracji dodatkowych systemów nadrzędnych i tu również całość sterowania można uprościć do jednostki sterującej robota.
Z racji, że dochodzi tu do kompletacji elementów ze statycznego pojemnika/skrzyni to komunikacja stanowiska z otoczeniem ogranicza się najcześciej do stanowisk następujących a nie poprzedzających.
Stosowane tu typu robotów najczęściej jednostki 6-osiowe konwencjonalne lub kolaboracyjne.
I tu zróbmy krótką przerwę.
Mam nadzieję, że podane przykłady pomogły Wam trochę lepiej zrozumieć jak działają poszczególne aplikacje i może będą stanowiły źródło inspiracji do poszukiwania Waszych własnych możliwości automatyzacji i robotyzacji.
Jeśli pomogłem to wiecie co zrobić.
Zostawcie łapkę w górę i zasubskrybujcie mój kanał na YT, Spotify czy Apple Podcasts – gdzie Wam wygodnie i gdzie aktualnie tego słuchacie
A tymczasem, życzę Wam spokojnego dnia i do usłyszenia za tydzień.
Cześć.