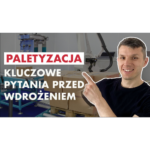
Witajcie na kanale Automatyzacja w Produkcji. Ja nazywam się Arkadiusz Pietrowiak.
Jestem CEO firmy Nixal. Na swoim kanale omawiam zagadnienia związane właśnie z
automatyzacją i robotyzacją produkcji w możliwie prosty i zrozumiały sposób.
Zapraszam do subskrybowania kanału i oglądania (lub słuchania) dzisiejszego odcinka.
Dopiero co skończyłem mówić o najpopularniejszych aplikacjach w Polsce, a już wracam aby jeden z tych tematów pogłębić. Opisanie 12 najpopularniejszych aplikacji zajęło mi aż 4 odcinki – średnio więc jakieś 2-3 minuty na każdą aplikację choć podział nie był tak równy i niektórym poświęciłem trochę więcej czasu. Założyłem jednak od razu, że przynajmniej do niektórych z wymienionych przykładów wrócę aby ten opis pogłębić. I to niniejszym dziś czynie.
Dziś będzie bowiem mowa o paletyzacji. Czyli jak już wcześniej zdążyłem powiedzieć o prawdopodobnie najpopularniejszej aplikacji w Polsce.
Dziś spojrzymy na to zagadnienie jednak dużo szerzej i z nieco innej perspektywy.
Przejdźmy więc do części merytorycznej dzisiejszego odcinka.
Przejdźmy więc do części merytorycznej dzisiejszego odcinka.
Jak to zpaletyzować – cz.1
Na początek zacznijmy od przypomnienia definicji, czyli czym ta paletyzacja w ogóle jest.
Paletyzacja jest procesem układania elementów, towarów na palecie.
Jak wspomniałem też ostatnio, obejmuje ona również wszystkie czynności niezbędne do wykonania, celem kompletacji gotowej do transportu jednostki paletowej czyli np:
- Magazynowanie i dostarczanie palet do miejsca paletyzacji
- Układanie przekładek i pozostałych elementów zabezpieczających towar oraz paletę
- W skład stanowisk paletyzacji nierzadko wchodzą też wszelakiego typu urządzenia foliujące i stretchujące, których celem jest zabezpieczenie towaru przed wypadnięciem z palety.
Naświetliłem tylko, że odwrotnością procesu paletyzacji jest depaletyzacja. Czyli proces odwrotny, a przez to też najczęściej dużo bardziej skomplikowany.
Dziś postaram się odpowiedzieć na te pytania, które zadaje sobie (albo na pewno powinien sobie zadać) prawdopodobnie każdy zastanawiający się nad zakupem i wdrożeniem stanowiska paletyzacji czyli np. Jakie rozwiązania techniczne jest najlepsze dla mnie? W co powinno być wyposażone stanowisko i kilka innych pytań…
Zacznijmy jednak od wprowadzenia pewnego zasadniczego podziału.
Przede wszystkim do paletyzacji możemy używać albo robota albo maszyny-manipulatora, potocznie zwanego paletyzatorem.
W zakresie maszyn paletyzujących czyli tzw. Paletyzatorów rozróżniamy przede wszystkim jego dwa typy – wspomniane wcześniej manipulatory oraz paletyzatory tzw. Płytowe lub stołowe (to ten sam typ urządzenia tylko różnie nazywany).
Zatrzymajmy się tu więc na chwilę i opiszmy to sobie trochę dokładniej.
Paletyzatory płytowe od manipulatorów różnią się przede wszystkim sposobem formowania warstwy. Manipulatory pobierają po 1 lub kilka paletyzowanych produktów, natomiast na stole paletyzatora stołowego formowana jest z reguły od razu cała warstwa produktu.
Manipulatory mogą przybierać najróżniejsze formy będące odzwierciedleniem z reguły podstawowych układów kinematycznych. Do najpopularniejszych należy układ kartezjański. W takim przypadku chwytak porusza się w trzech osiach wzajemnie prostopadłych tzw XYZ. Czasem może pojawić się dodatkowa oś obrotowa chwytaka.
Drugim, jednak już istotnie mniej popularnym, jest układ cylindryczny. W takim wypadku mamy do czynienia z obrotową podstawą oraz dwoma osiami postępowymi tzn. Z ruchem w pionie i poziomie. W przypadku takiej kinematyki jest większe prawdopodobieństwo zapotrzebowania na dodatkową oś obrotową w chwytaku gdyż bez tego właściwe ułożenie produktów może się okazać niewykonalne.
Tego typu manipulatory w paletyzacji obecnie stosuje się niezwykle rzadko. Przesłanką do ich użycia może być m.in bardzo specyficzna konstrukcja obiektu uniemożliwiającą zastosowania innych rozwiązań. Z racji, że tego typu urządzenia są często konstrukcjami projektowanymi pod konkretne zastosowanie to można je dzięki temu względnie dowolnie ukształtować i spersonalizować. Z tego też względu dodatkowym powodem może być duża lub mała masa obiektów przenoszonych. Najbardziej standardowe manipulatory do małych mas prawdopodobnie będą mogły konkurować cenowo i być nieco korzystniejsze kosztowo niż roboty. Jeśli jednak mamy do czynienia z dużą masą obiektu to taki manipulator można wykonać w wersji o udźwigu większym niż jakikolwiek dostępny na rynku robot. I w tym obszarze, to rozwiązanie może okazać się bezkonkurencyjne.
Przejdźmy do drugiej grupy paletyzatorów maszynowych czyli tzw. Paletyzatorów płytowych – i trzymajmy się już tej nazwy do końca.
Zasada działania tego urządzenia opiera się na tym, że produkty są formowane w pełnych warstwach na stole zbudowanym najczęściej z jednej lub dwóch płyt. Stół zapewnia wymagane ograniczenia kształtowe, które utrzymują warstwę w ustalonym kształcie. Po jej pełnym uformowaniu płyta lub płyty stołu wysuwają się spod warstwy, a produkty spadają na paletę, tworząc tam kolejną jej warstwę.
W tego typu urządzeniach najcześciej nie mamy żadnych chwytaków – najczęściej bo i te się zdarzają. Co do zasady jednak projekt formowany jest przepływowo. Kolejno najeżdżające produkty są odpowiednio nakierowywane lub obracane przez znajdujące się na trasie bandy. W konstrukcyjnie bardziej skomplikowanych rozwiązaniach produkt jest obracany przez małe manipulatory z chwytakiem – ale to raczej niszowe rozwiązanie w tych urządzeniach.
Warstwa palety z produktów formowana jest najczęściej w jednym miejscu, by następnie cała warstwa została przesunięta na wcześniej wspomniany stół płytowy.
Pod takim stołem znajduje się prosta, często łańcuchowa winda, która unosi paletę wypełnianą kolejnymi warstwami. Winda „podwozi” paletę bezpośrednio pod stół. Stół się rozsuwa i produkty spadają. Po uformowaniu całej palety winda „zwozi” paletę na przenośnik i ta opuszcza urządzenie.
Paletyzatory płytowe były bardzo popularne w latach 70, 80 i 90. Od tego czasu sukcesywnie wypierane są przez roboty przemysłowe. W dalszym ciągu jednak są zastosowania, w których paletyzator płytowy ma istotną przewagę nad rozwiązaniem zrobotyzowanym. Przykładem takiej sytuacji jest np. wydajna i powtarzalna produkcja produktów w długim okresie (tj. Kilku-kilkunastu lat) w mocno ograniczonej ilości typów opakowań. W takim przypadku paletyzator płytowy sprawdzi się bardzo dobrze. Korzyści dodatkowo rosną gdy mamy do czynienia z produktem trudnym w formowaniu – np. workami wypełnionymi ziarnem, cukrem lub jakimkolwiek innym materiałem sypkim. Stół paletyzatora płytowego dobrze formuje warstwy mające tendencję do „rozłażenia się” i odbywa się to bez utraty wydajności.
Paletyzator płytowy jest rozwiązaniem nieco mniej „szytym na miarę” niż manipulator, ale jednak wprowadzenie modyfikacji jest pracą czysto mechaniczną, a więc i nieco skomplikowaną. Zmiana produktu czy układu produktów na warstwie może wymagać więcej pracy niż zmiana programu, a czasem może być wręcz niemożliwa bez szlifierki i spawarki.
Paletyzator płytowy ma dość duży współczynnik kosztu stałego przez co w prostych aplikacjach, o niewymagającej wydajności, będzie przegrywał z pozostałymi rozwiązaniami. Jednak im większa wydajność tym różnica kosztów wdrożenia będzie maleć, a przy naprawdę dużych wydajnościach i ciężkich produktach robot może (choć nie musi) te rywalizację kosztową przegrać.
To by było na tyle jeśli chodzi o rozwiązania stricte mechaniczne.
Przyjrzymy się zatem paletyzacji z użyciem robotów przemysłowych.
Pierwszym i podstawowym typem podziału w tej grupie jest podział na aplikacje zrealizowane z użyciem robotów konwencjonalnych i kolaboracyjnych. Zacznijmy jednak od tych pierwszych.
Jak wspomniałem już w poprzednim odcinku, producenci robotów posiadają w swojej ofercie roboty dedykowane do paletyzacji i to z ich użyciem realizowana jest większość stanowisk tego typu.
Robot przeznaczony do paletyzacji ma, tak jak wspomniany wcześniej manipulator, najczęściej 4 osie. W odróżnieniu jednak od manipulatora wszystkie osie są osiami obrotowymi co daje nam zupełnie inną, bliższą strefę dostępnych przemieszczeń i osiąganych pozycji.
Roboty paletyzujące charakteryzują się też większymi udźwigami – dostępne na rynku konstrukcje pozwalają na udźwig od 100 do 300kg. Oczywiście, gdy mówimy o udźwigu robota to podana wartość jest wartością maksymalną wyznaczoną na samej kiści (tzw. Końcu robota). Każde odsuniecie środka ciężkości od tego punktu powoduje zmniejszenie maksymalnego możliwego udźwigu robota. I co najważniejsze – podana masa obejmuje też chwytak. Chwytaki do paletyzacji ważą z reguły 50-100 kg zależnie do funkcjonalności i masy przenoszonych produktów. Warto mieć to na uwadze dobierając robota do produktu.
Roboty do paletyzacji dostarczane są też nierzadko z oprogramowaniem do paletyzacji dedykowanym – co potencjalnie może skrócić czas programowania i późniejszych modyfikacji programowych, gdyż korzysta się w tym przypadku z gotowych bloków programowych.
Jeśli zamierzasz wdrożyć zrobotyzowane stanowisko paletyzujące w 2023 roku to prawie na pewno aplikacja zbudowana w oparciu o 4-osiowego robota paletyzującego będzie najlepszym wyborem dającym dużą swobodę dodawania dodatkowych funkcjonalności i przyszłych modyfikacji. O ile produkcja nie odbywa się w zabójczym tempie to również można założyć, że ten robot sprosta oczekiwanej wydajności. A do tego dogada się ze wszystkimi urządzeniami współpracującymi.
Idąc dalej w obszarze robotów konwencjonalnych. Zdarzają się również aplikacje zrobotyzowane, które do paletyzacji wykorzystują standardowe roboty 6-osiowe. Jedynym znanym mi sensownym uzasadnieniem stosowania tego typu robotów w paletyzacji jest potencjalna konieczność wykonania dodatkowych operacji lub reorientacji produktu. Przykładem takiej dodatkowej operacji może być naklejanie etykiety na paletę lub bezpośrednio na produkt i to właśnie w taki sposób, który wymaga jego obrócenia. Żeby to jeszcze miało sens to sam produkt musi być stosunkowo lekki – tj. Max 10-15kg. Powyżej tej wartości koszty robota będą już najpewniej przewyższać koszty zastosowania robota 4-osiowego z dodatkowym osprzętem. Innym esktremalnym przypadkiem, w którym robot 6-osiowy byłby dobrym rozwiązaniem jest sytuacja, w której zachodzi konieczność omijania jakichś elementów krajobrazu typu słup czy belka sufitowa. Ruchliwość kinematyki 6-osiowej pozwoli na stworzenie trajektorii omijającej przeszkodę co w przypadku robota 4-osiowego mogłoby być niemożliwe. Zdarzają się takie przypadki, gdy ilość miejsca jest tak mała, że taka gimnastyka jest koniecznością nie widzimisię – ale to promil przypadków. Sam widziałem ledwie 3 tego typu aplikacje.
W obszarze robotów konwencjonalnych mamy jeszcze dwa typu robotów – scara oraz delta.
Nie są to rozwiązania, które powszechnie stosuje się do paletyzacji ze względu na ich zasięg i udźwig. Przynajmniej tak długo, gdy pod pojęciem paletyzacji rozumiemy układanie na palecie. W procesach pakowania te roboty występują bowiem bardzo często. Nominalne udźwigi tych robotów to najczęściej kilka kg – maksymalnie do 20 w największych konstrukcjach. Zasięgi przekraczające metr również występują w mniejszości, szczególnie w kinematyce typu scara. Dlatego, aby takimi robotami prowadzić skuteczną paletyzację musiałby być one umieszczone bezpośrednio nad paletą, aby ogarnąć ją całą swoim zasięgiem. A żeby to wszystko miało sens, produkt musiałby być mały i lekki, a wydajność jednostkowa duża. W praktyce małe i lekkie produkty najczęściej pakowana są w większe zbiorcze opakowania co przekłada się na stabilność palety w transporcie. Do tej pory nie zdarzyło mi się takiego rozwiązania zobaczyć nigdzie poza jutubem co już chyba też o czymś świadczy. Ale jednoznacznie należy powiedzieć, że taka aplikacja jest wykonywalna.
I mamy też ostatnią grupę – roboty kolaboracyjne.
W tej grupie mamy do czynienia głównie, przyjmijmy, że tylko, z robotami przegubowymi 6-osiowymi. Od robotów konwencjonalnych różnią się one przede wszystkim:
1) Mniejszym maksymalnym zasięgiem – praktycznie rzadko przekraczającym 1,5 metra
2) Mniejszym maksymalnym udźwigiem – zamykającym się z reguły w przedziale 5-15kg, bardzo rzadko dobijającym do 20kg.
3) Kolabarocyjnością właśnie – kiedy robot można nazwać kolaboracyjnym i jakie funkcjonalności techniczne o tym decydują, tym zajmiemy się przy innej okazji. Na ten moment wystarczy nam założenie, że robot kolaboracyjny to taki, który w wyniki kolizji z jakimkolwiek obiektem na swojej trajektorii ruchu (np. Człowiekiem) uderza w niego znormalizowaną siłą, nie czyniąc mu krzywdy, po czym się zatrzymuje. Różni się tym od robota konwencjonalnego, który takiego człowieka na swojej trasie traktuje nieporównywalnie większą siłą, która jeszcze rośnie, dopóki „korki” w robocie się nie wysprzęglą. Innymi słowy – trudniej takie spotkanie wtedy przetrwać.
Dzięki tej kolaboracyjności, coboty mogą, z zachowaniem wytycznych i w zgodności z normami, pracować bez wygrodzeń bezpieczeństwa.
Normy ograniczają jednak maksymalną prędkość przemieszczeń cobota przez co maksymalne prędkości cobota to nawet 10% prędkości maksymalnych robotów konwencjonalnych.
Dodatkowo, aby robot był bezpieczny dla otoczenia, bezpieczny musi też być chwytak. Przez to nierzadko, aby ten cel osiągnąć, należy korzystać z gotowych, dość drogich rozwiązań.
Mamy więc 3 cechy robotów kolaboracyjnych – niewielki udźwig i zasięg oraz możliwość pracy w otoczeniu ludzi. Wniosek z tego można wysnuć dość łatwo – tego typu aplikacje są bardzo fajne gdy paletyzujemy niewielkie i lekkie produkty z niezbyt dużą wydajnością. Jednocześnie korzyści z ich zastosowania rosną gdy miejsca jest zbyt mało na wygrodzenie lub zależy nam na mobilności rozwiązania bo np. Często będzie ono przemieszczane w różne lokalizacje zakładu.
I tu, mając solidną dawkę podstawowych definicji, zróbmy krótką przerwę – na tydzień.
Liczę, że dowiedzieliście się dzisiaj czegoś nowego albo przynajmniej uporządkowaliście sobie posiadaną już wiedzę.
Już standardowo…Jeśli macie Swoje przemyślenia na ten temat lub po prostu uważacie, że pominąłem jakiś ważny szczegół to zapraszam do pisania do mnie w tej sprawie.
Jeśli się Wam podobało to wiecie co zrobić.
Zostawcie łapkę w górę i zasubskrybujcie mój kanał na YT, Spotify czy apple podcasts – gdzie Wam wygodnie i gdzie aktualnie tego słuchacie.
A tymczasem, życzę Wam spokojnego dnia i do usłyszenia za tydzień.
Cześć.