Problemy przedsiębiorstwa
Podczas wizyty u Inwestora zdefiniowano, iż największym problemem z jakim się mierzy są braki kadrowe wpływające bezpośrednio na wydajność linii. W wyniku problemów kadrowych ręczne maszyny nie mogą zapewnić zakładanej wydajności, szczególnie, że praca przy opisywanym produkcie ma charakter sezonowy. Dodatkowo w przypadku opracowywania większej ilości zapasów dochodzi do zbrylenia produktów w workach co jest niedopuszczalne dla Inwestora.
PROBLEMY PRZEDSIĘBIORSTWA
- Paletyzacja worków z wagopakowaczki i z depaletyzacji przez min. 5 osób na zmianę.
- Depaletyzacja ciężkich 50 kilogramowych worków.
- Zbrylanie produktu w workach spowodowane koniecznością magazynowania dużej ilości produktów.
- Problemy kadrowe.
- Przestoje wynikające z problemów wydajnościowych.
POTRZEBY PRZEDSIĘBIORSTWA
- Zwiększenie wydajności o minimum 47%, przy zachowaniu obecnej obsady.
- Rozbrylony produkt w workach.
- Depaletyzacja worków w celu rozbrylenia, bez uszkadzania worka.
- Zmniejszenie ilości potrzebnych pracowników na stanowisku,
- Paletyzacja worków jutowych.
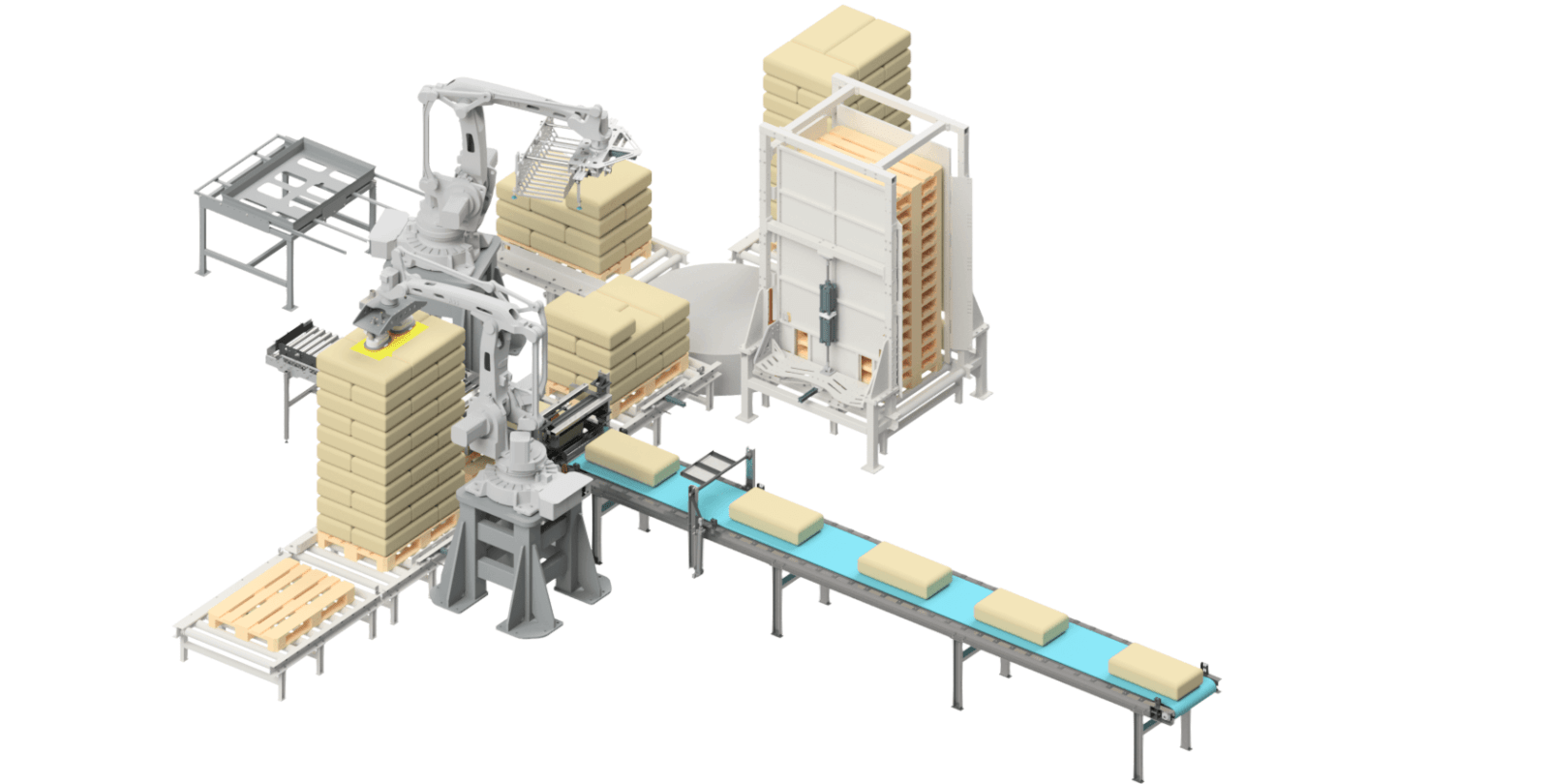
ANALIZA POTRZEB
Opracowane rozwiązanie powinno zwiększać wydajność systemu o minimum 47% co pozwoli na zmniejszenie ilości magazynowanych palet do minimum. Dzięki takiemu rozwiązaniu możliwe będzie dostarczanie do klienta końcowego świeżego produktu o znacznie lepszych parametrach jakościowych. Dostarczany system powinien wykonywać zadania związane z paletyzacją, depaletyzacją, rozbrylaniem i stackowaniem gotowych zapakowanych palet. Końcowym założeniem było owinięcie palety folią stretch lub nałożenie kaptura foliowego.
WERYFIKACJA ZAŁOŻEŃ
Linia produkcyjna została poddana dogłębnej analizie, z której wynikało, iż największym wyzwaniem projektowym będzie depaletyzacja worków jutowych bez ich uszkadzania. Podjęto decyzję, iż w celach upewnienia się o poprawności założeń, należy wykonać testy. Dodatkowo z uwagi na ilość miejsca i ustalony budżet inwestycji zrezygnowano z owijania palety folią stretch w sposób automatyczny. Pozostano przy procesie półautomatycznym, polegającym na wykorzystaniu owijarki, którą posiadał Inwestor.
REALIZACJA
POZNAJ ETAPY NASZYCH PRAC
WIĘKSZA WYDAJNOŚC FIRMY
ROZWIĄZANE PROBLEMY
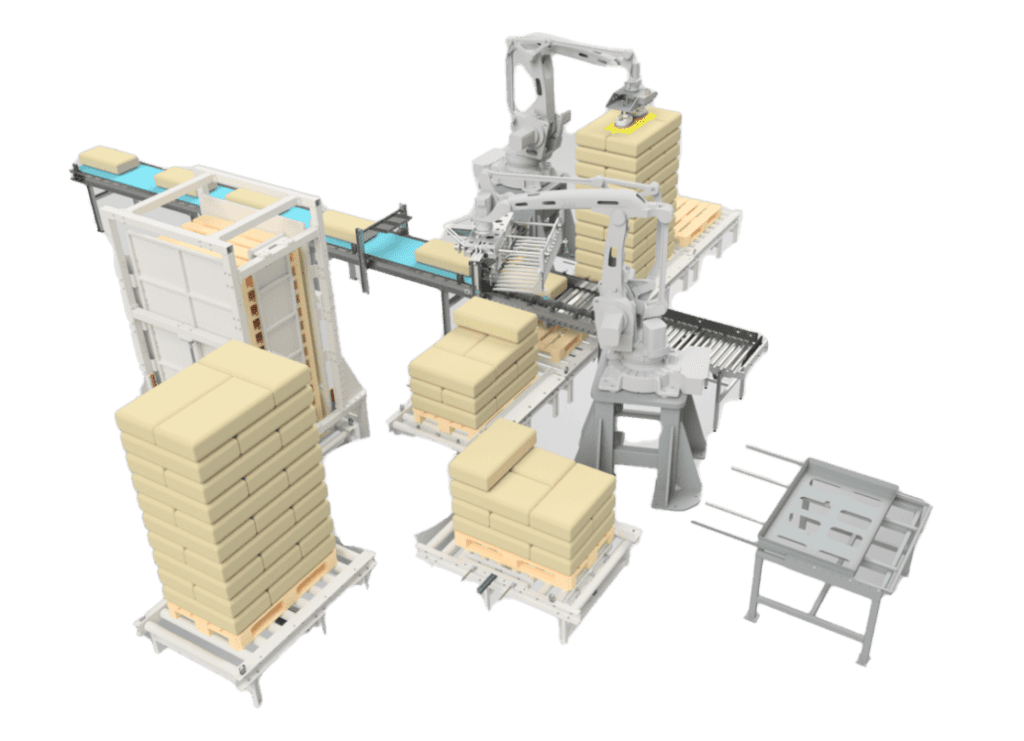
Po wykonaniu testów podjęto decyzję, iż depaletyzacja oparta tylko na ssawce podciśnieniowej może prowadzić do znacznego spadku wydajności, a w skrajnych przypadkach do upadania worków. Zdecydowano się na połączenie chwytaka widłowego z podciśnieniem co zwiększyło stabilność systemu. Inwestycja pozwoliła spełnić wszystkie potrzeby przedsiębiorstwa tzn.:
- zwiększono wydajność o 47%,
- zmniejszono zapotrzebowanie pracowników na tym stanowisku z 5 osób do 1 osoby na zmianę,
- uzyskano rozbrylony produkt w workach,
- paletyzację oraz depaletyzację worków bez ich uszkodzenia.
WDROŻONE ELEMENTY
SKŁADOWE SYSTEMU
- Przenośnik dostarczający worki z wagopakowaczki / odbierający z depaletyzacji,
- przenośnik roztrząsający produkt w worku,
- przenośnik odbiorczy dla robota paletyzującego,
- przenośnik odbierający palety z magazynu (do depaletyzacji),
- przenośnik depaletyzacji,
- robot i chwytak do depaletyzacji,
- przenośnik przejazdowy,
- robot paletyzujący i przenośnik do paletyzacji,
- chwytak widłowy do paletyzacji,
- magazyn przekładek tekturowych,
- magazyn pustych palet euro (na co najmniej 15 szt.),
- obrotnica,
- przenośnik palet na magazyn,
- przenośnik odbiorczy do palet do klienta.
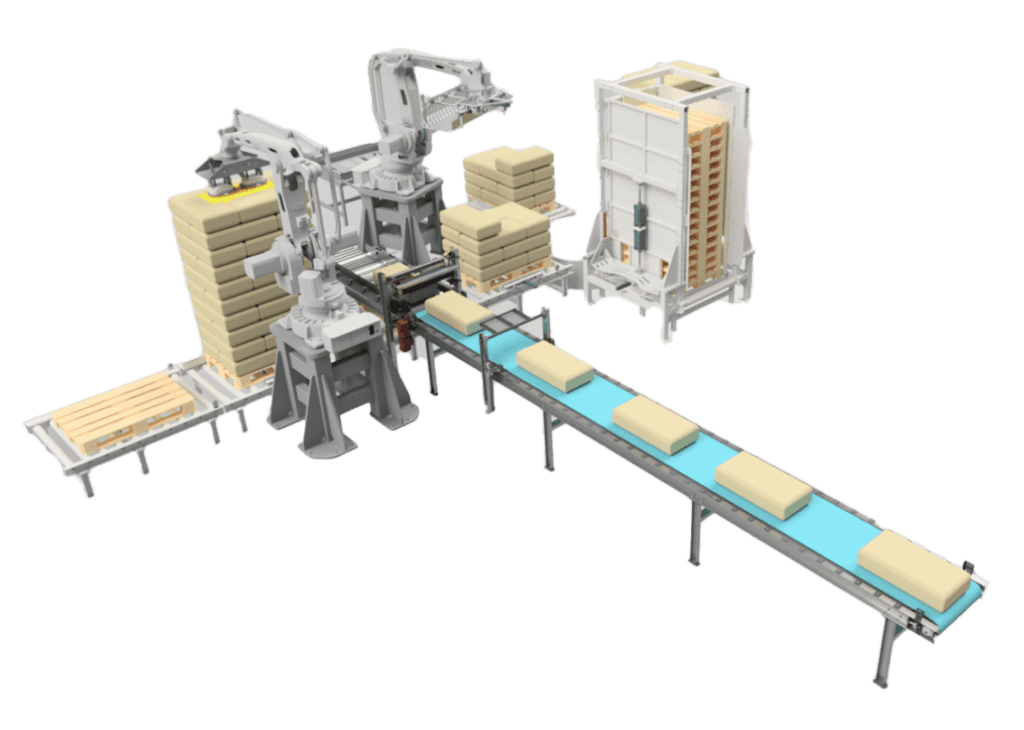