PROBLEMY PRZEDSIĘBIORSTWA
- Różne rodzaje palet w procesie paletyzacji.
- Niska wydajność spowodowana transportem towarów na wózkach widłowych.
- Ograniczony system transportu towarów.
- Przestoje spowodowane niewystarczającą liczbą operatorów wózków widłowych.
POTRZEBY PRZEDSIĘBIORSTWA
- System przenośników pozwalający na transport towarów pojedynczo oraz na paletach.
- Obsługa systemu przez maksymalnie dwóch operatorów wózków widłowych.
- Bezobsługowe układanie stosu produktów na obsługiwanych paletach.
- Dodatkowe wyposażenie w postaci owijarki do palet.
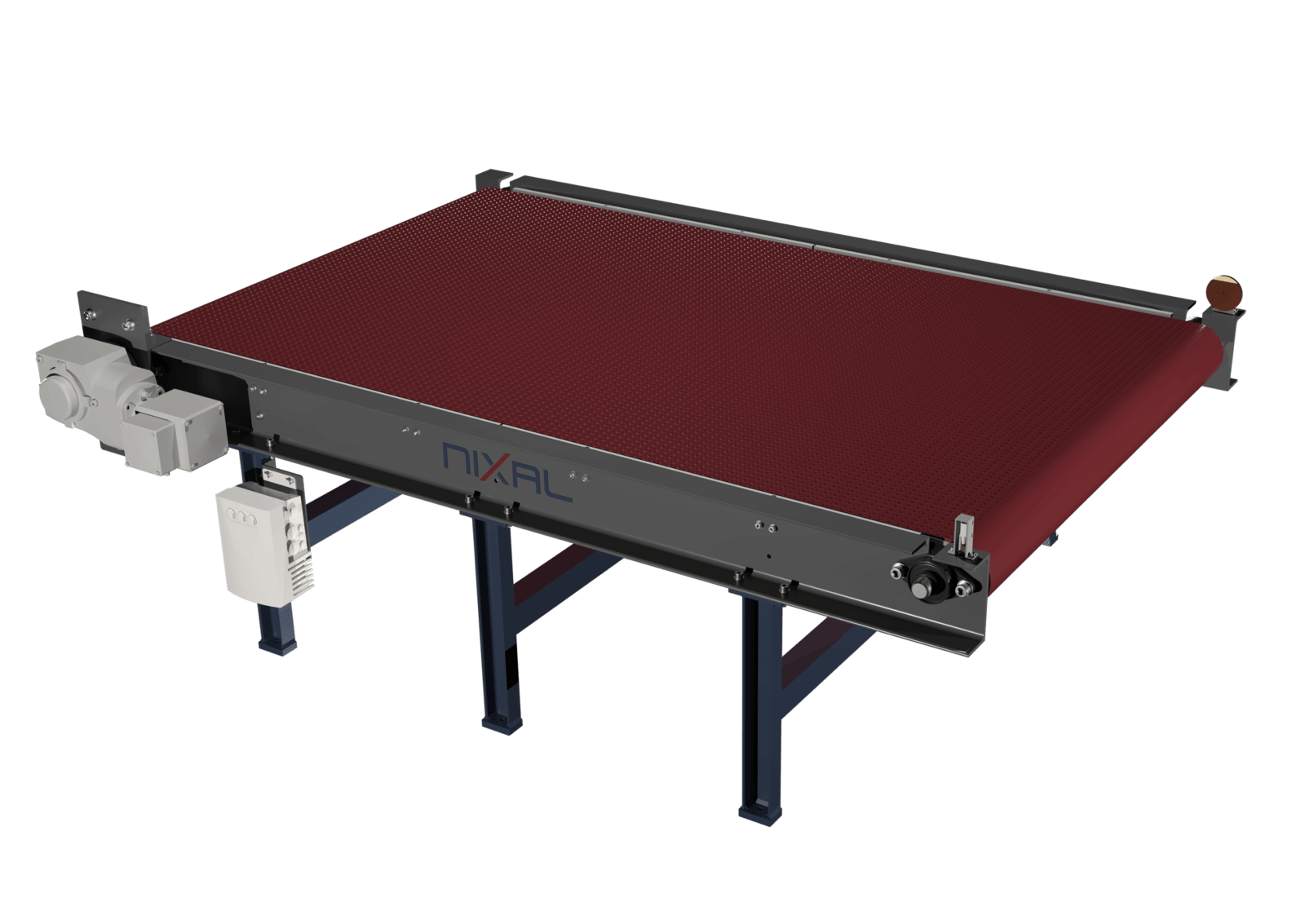
ANALIZA POTRZEB
Podczas pierwszych spotkań z Klientem zidentyfikowano, że największym problemem są braki kadrowe na stanowiskach operatora wózka widłowego. Braki te przyczyniły się do przestojów już na etapie odbioru towarów z wózków widłowych. Kolejnym problemem był fakt, że Klienci Inwestora zamawiali towar na różnego rodzaju paletach, co generowało dodatkowe opóźnienia i przestoje. Dodatkowo czas potrzebny na transport elementów między halami produkcyjnymi, a magazynem znacząco obniżał wydajność przedsiębiorstwa.
WERYFIKACJA ZAŁOŻEŃ
Uszeregowano listę problemów przedsiębiorstwa według priorytetów wdrożenia projektu. Założeniem inwestora było dostarczenie palet z magazynu palet do miejsca, w którym układano na nich produkty. Całość miała być transportowana do magazynu. Po przeprowadzeniu symulacji okazało się, że rozwiązanie to nie poprawi wydajności procesu. Zaproponowaliśmy, aby produkty z różnych linii były transportowane do miejsca ich paletyzacji. Zarówno proces paletyzacji, jak i magazyny różnych rodzajów palet znajdują się na tej samej hali. Dodatkowo do układania produktów w stosy wykorzystano windy, które pozwalają na bardziej ergonomiczną pracę operatorów maszyn. Obliczono również, że do zwiększenia wydajności wystarczy dwóch operatorów wózków widłowych zamiast dotychczasowych 6 osób.
REALIZACJA
POZNAJ ETAPY NASZYCH PRAC
WIĘKSZA WYDAJNOŚC FIRMY
ROZWIĄZANE PROBLEMY
- Wydajność procesu została zwiększona dwukrotnie.
- Eliminacja problemów związanych z brakami kadrowymi.
- Czas samego transportu został skrócony o 67%!
- Poprawiono ergonomię pracy operatorów wózków widłowych.
- Eliminacja przestojów produkcyjnych.
WDROŻONE ELEMENTY
SKŁADOWE SYSTEMU
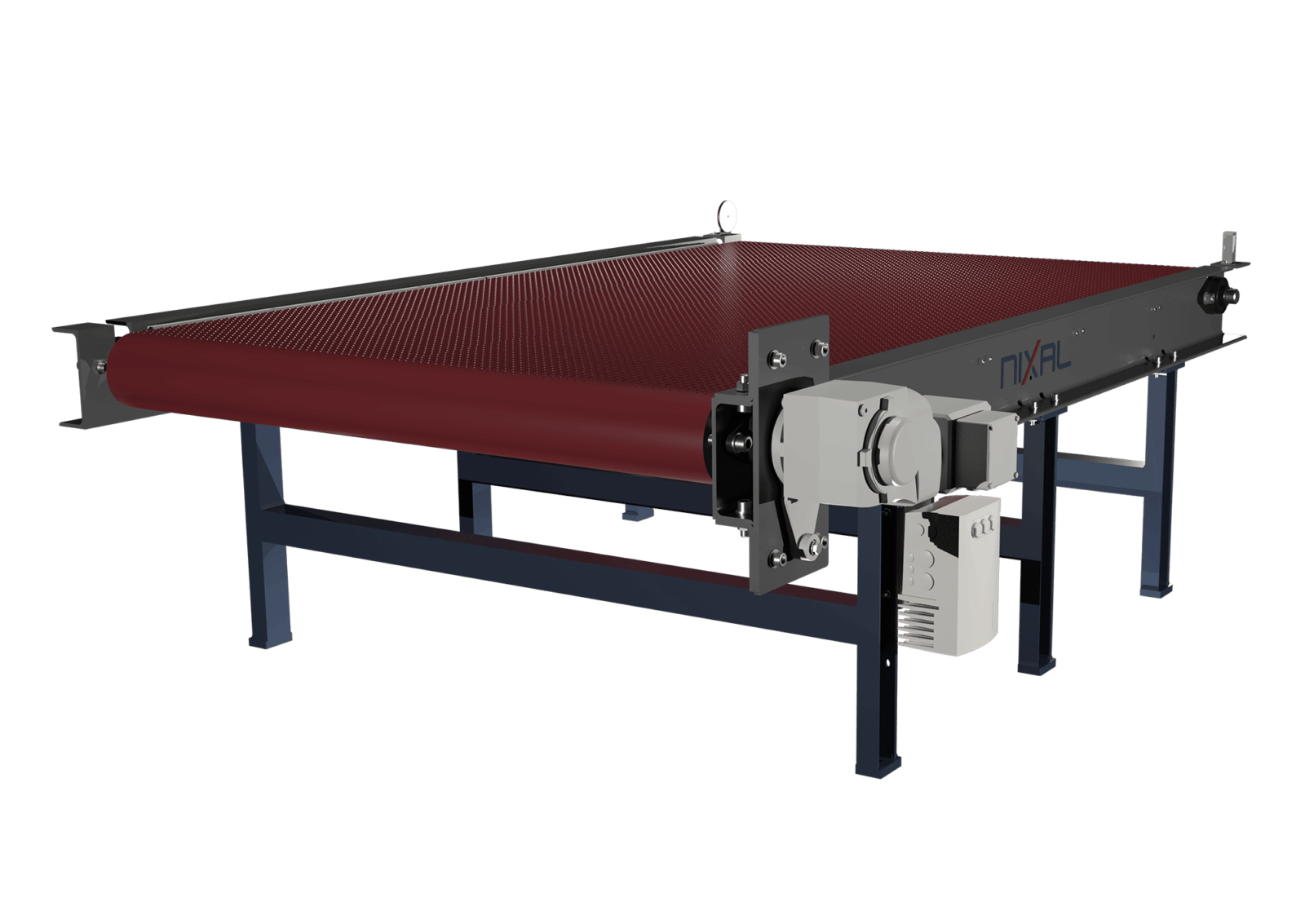
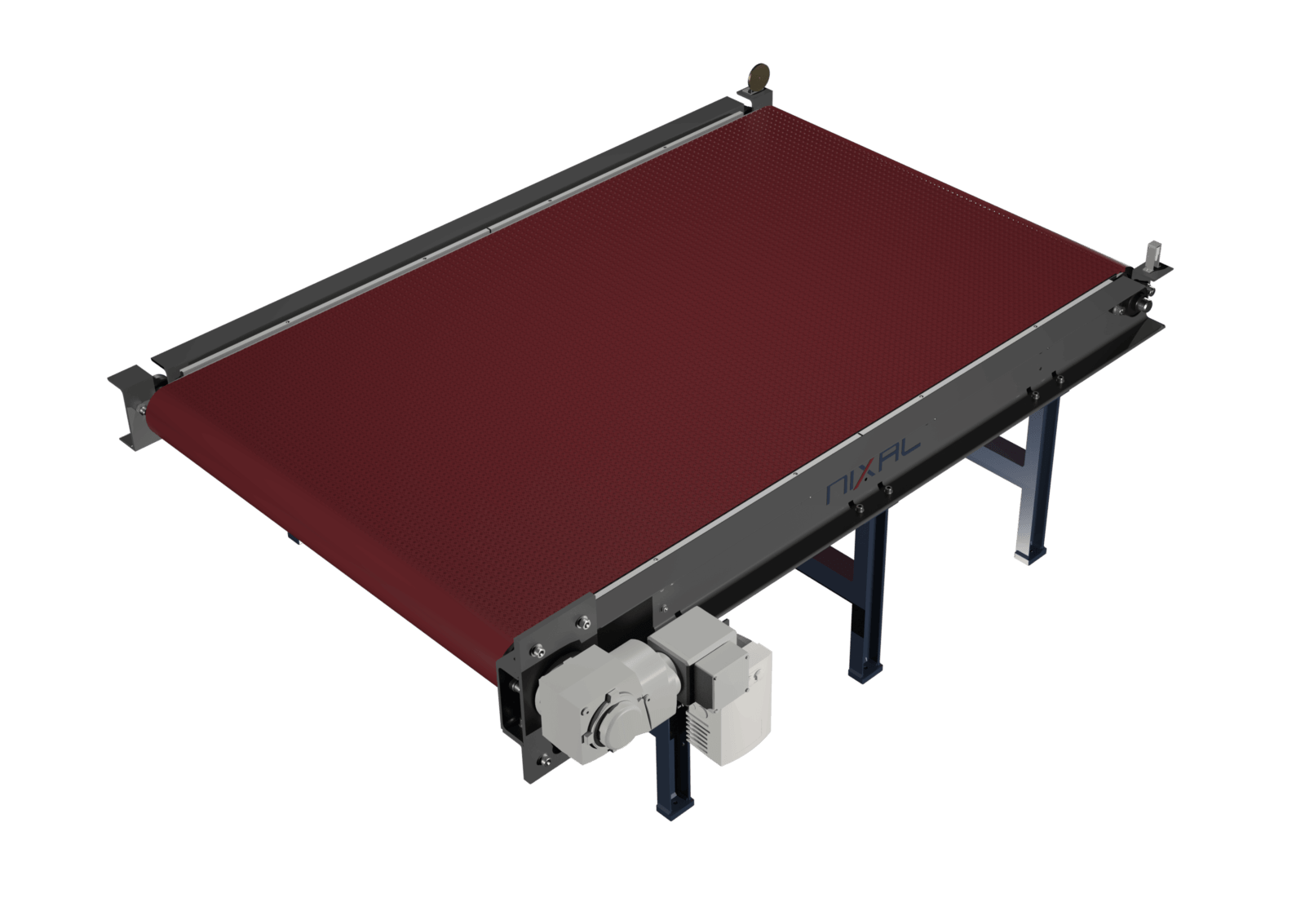
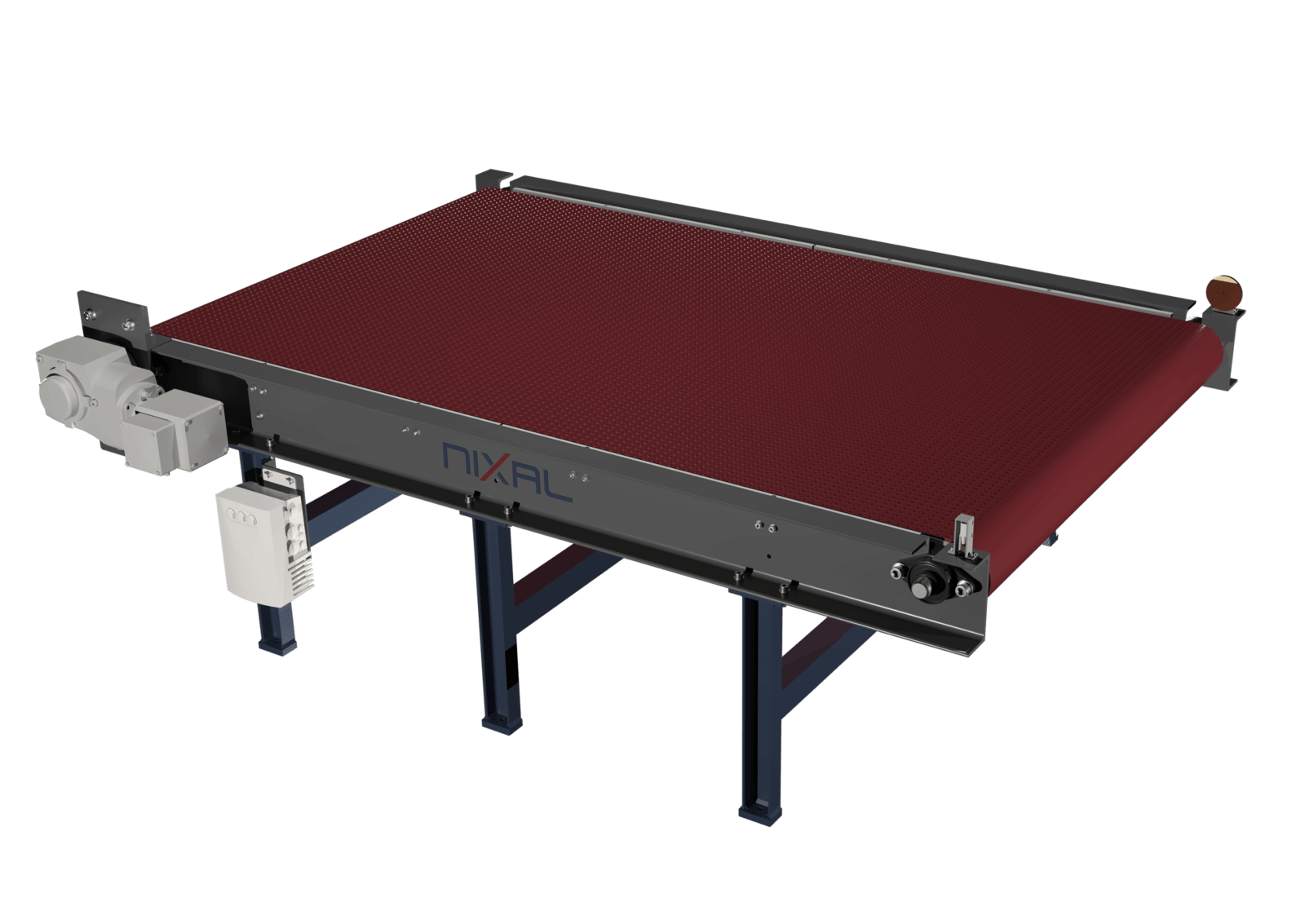
- przenośniki modułowe do transportu dużych gabarytów
- winda do pokonania różnicy poziomów na hali
- 5 magazynów palet
- paletyzator
- owijarka
- przenośniki rolkowe do transportu palet
- 3 windy do poprawy ergonomii na stanowiskach pracy